Hello David. Allen here. As someone who lives and breathes electric mobility from the factory floor, I often speak with partners like you who are navigating the market. A question that frequently comes up, both from distributors and the final customers, is about the significant price tag on cargo bikes. You look at a cargo bike, then at a standard commuter bicycle, and the difference in cost can be surprising. Why is that?
This isn’t just a simple case of a bigger frame. The reality is that a cargo bike is a highly specialized piece of engineering, often designed to replace a car for many daily tasks. In this article, I want to pull back the curtain and give you a manufacturer’s perspective. We’ll break down exactly what goes into the bike cost, from the raw materials and specialized components to the complex research and development and rigorous safety testing. Understanding these factors will not only clarify why cargo bikes are so expensive but also highlight the incredible value and capability they offer. This is the information you need to confidently explain the investment to your own network.
What Exactly is a Cargo Bike and How Does It Differ from a Regular Bicycle?
At its core, a cargo bike is any cycle specifically designed to carry more than just its rider. While a regular bicycle might have a small rack for a bag, cargo bikes are designed to transport significant loads, whether that’s a week’s worth of groceries, commercial goods for a delivery business, or even your three kids. This fundamental difference in purpose dictates a completely different approach to design and engineering compared to traditional bicycles.
There are a few main types of cargo bikes you’ll see in the bike market:
- Longtails: These look the most like a standard bicycle but have an extended rear frame (a longer wheelbase) with a built-in rack to accommodate passengers, child seats, or large panniers.
- Front-Loaders (Bakfiets/Long Johns): These feature a large cargo box or platform situated between the handlebars and the front wheel. This design keeps the load low to the ground for excellent stability, making it a great option for carrying children or bulky items.
- Tricycles (Trikes): These three-wheeled wonders, like our MINI TRUCK 1.5m electric 3wheels electric ebike, offer maximum stability, especially when stopped. They are a popular choice for delivery fleets and families who want the easiest possible riding experience when hauling a heavy load.
The key takeaway is that a cargo bike is not just a beefed-up bicycle. It’s a purpose-built utility vehicle. Every component, from the frame to the spoke in the wheel, is chosen and engineered to handle the unique demands placed on it, which is the first step in understanding its cost.
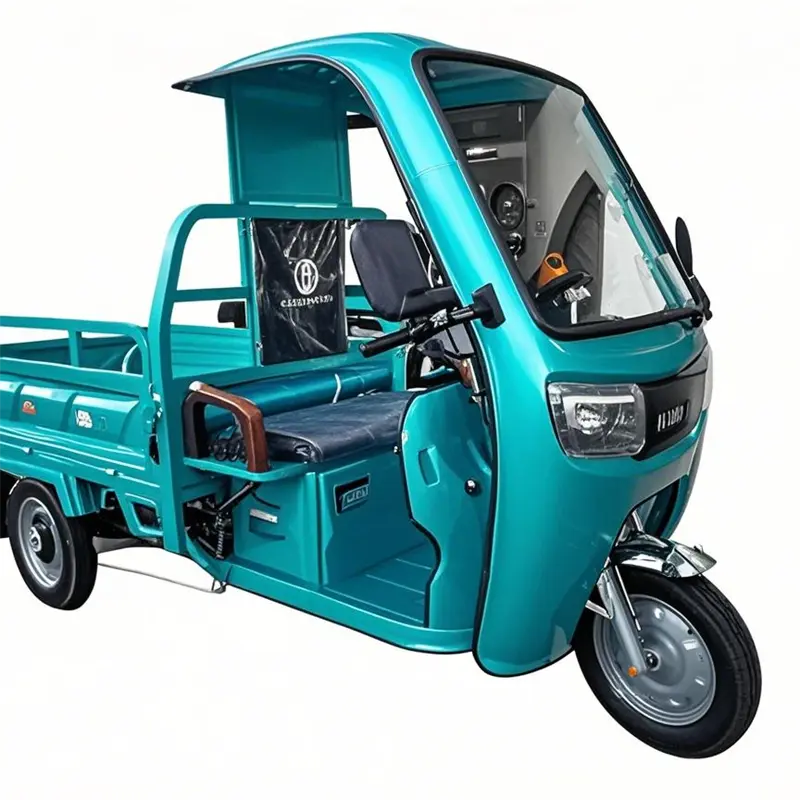
Why Are Specialized Components the Biggest Factor in Why Cargo Bikes Are So Expensive?
When you ask, “Why are bikes so expensive?”, the answer often lies in the components. This is magnified tenfold for a cargo bike. You simply cannot use standard bicycle parts and expect them to hold up under the stress of carrying an extra 100-200 kg. From our perspective as manufacturers, sourcing and integrating these heavy-duty parts is a primary driver of the higher price.
Think about the frame. It’s not just longer; it’s built with thicker-gauge tubing and extra gussets to prevent flexing and ensure stability. The brake systems are another critical area. Standard rim brakes are inadequate. A fully loaded cargo bike needs powerful, reliable stopping power, which is why hydraulic disc brakes are the standard. These systems offer superior performance in all weather conditions but also contribute significantly to the overall cost. Then there are the wheels, which must be stronger, with more robust rims, thicker spokes, and high-volume tires to handle the weight and smooth out the ride.
Here’s a simple table to illustrate the difference:
Component | Standard Bicycle | Heavy-Duty Cargo Bike | Why it Costs More |
---|---|---|---|
Frame | Lightweight Aluminum/Steel | Reinforced, Oversized Tubing | More material, complex welding, stress-testing. |
Brakes | Rim Brakes / Mechanical Disc | 4-Piston Hydraulic Disc Brakes | Superior power, heat dissipation, and reliability. |
Wheels | 32-Spoke Standard Rims | 36/48-Spoke Double-Wall Rims | Increased strength and durability to prevent failure under load. |
Kickstand | Simple Side Kickstand | Dual-Leg Center Stand | Must support hundreds of pounds stably for safe loading/unloading. |
Tires | Standard Commuter/Road Tires | Puncture-Resistant, High-Volume | Designed to carry weight, improve comfort, and reduce flats. |
Each of these upgrades adds to the final price. We cannot compromise on these elements. For a business like yours, David, delivering a product that is safe and durable is paramount for customer satisfaction and brand reputation. That quality starts with these foundational, specialized components.
How Does an Electric Motor Turn a Cargo Bike into a Powerful E-Cargo Machine?
Now, let’s add electricity to the equation. The electric cargo bike, or e-cargo bike, is a game-changer, but it also significantly increases the cost. The electric assist system isn’t just a small motor tacked on; it’s a powerful, integrated drivetrain designed to make hauling heavy loads feel almost effortless. Without it, moving a fully loaded cargo bike, especially uphill, would require superhuman strength.
The motor itself is a major expense. While some budget models use hub motors, many cargo bikes opt for a mid-drive motor. Mid-drive systems, which apply power directly to the crank, are more efficient, provide a more natural riding experience, and are better at tackling hills when you carry heavy loads. They are also more complex and expensive. The other half of the equation is the battery. Cargo e-bikes require high-capacity batteries to provide a useful range. A small battery that works for a lightweight commuter ebike would be drained in minutes on an e-cargo bike. We use batteries that are larger, use high-quality cells (from brands like Samsung or LG), and are housed in durable, often weatherproof casings.
Furthermore, for the US market, UL certification for the battery and electrical system is non-negotiable. This certification process is expensive for us as manufacturers, but it’s a critical guarantee of safety against fire risks. When you’re dealing with high-capacity lithium-ion batteries, this is an investment in safety that no responsible brand would ever skip. The combination of a powerful mid-drive motor, a large and certified battery, and the associated controller and display easily adds over a thousand dollars to the cost compared to regular bikes that are unassisted.
What Role Does Research and Development Play in the Final Price Tag?
A great cargo bike doesn’t just happen. It’s the result of countless hours of research and development. The engineering challenges are significant: how do you create a cycle that is long and strong enough to carry cargo, yet still nimble and safe to ride? How do you balance the weight perfectly so it doesn’t become unwieldy? These are questions our engineers spend months, sometimes years, solving.
The R&D process involves:
- Computer-Aided Design (CAD): Creating detailed 3D models to test geometry and stress points virtually.
- Prototyping: Building physical models to test in the real world. This is an iterative process of building, testing, refining, and rebuilding. A new cargo bike might go through dozens of prototype stages.
- Component Integration: Ensuring the frame, motor, battery, and all other parts work together seamlessly. This is especially complex for an electric cargo bike.
- Ride Testing: Employing test riders to put the bikes through their paces in various conditions to fine-tune the handling and riding experience.
All this innovation costs money. The salaries of skilled engineers, the cost of materials for prototypes, and the extensive testing all get factored into the price of a cargo bike. While a large brand might spread these costs over hundreds of thousands of standard bikes, the cargo bike market is a more niche market. This means the R&D costs are amortized over a smaller number of units, which naturally makes each bike might cost more.
Are Safety Certifications and Testing a Major Contributor to the Higher Cost?
Absolutely. And for good reason. As a distributor, your biggest liability risk is an unsafe product. For us as a manufacturer, our reputation depends on it. A cargo bike is often used for carrying kids, so child safety is our top priority. This is why we invest heavily in testing and certification, and these higher costs are reflected in the final price.
The primary standard for e-bikes in Europe is EN 15194, and in the US, products must comply with CPSC regulations. For cargo bikes, especially those equipped with electric systems, the testing goes even further. We conduct rigorous stress tests on the frame, fork, and kickstand to ensure they can handle well beyond their stated weight limits. The brake systems are tested for endurance and stopping distance under full load. The electrical system, as mentioned, undergoes testing for standards like UL 2849 to ensure it’s safe from electrical and fire hazards.
This isn’t just a box-ticking exercise. It involves sending bikes to third-party labs, paying significant fees, and sometimes having to re-engineer components that don’t meet the standard. While this adds to the expense, it’s a non-negotiable part of building a trustworthy and reliable cargo bike. When you see those certification marks on a cargo bike, you’re not just seeing a sticker; you’re seeing an assurance of safety that has been paid for and earned.
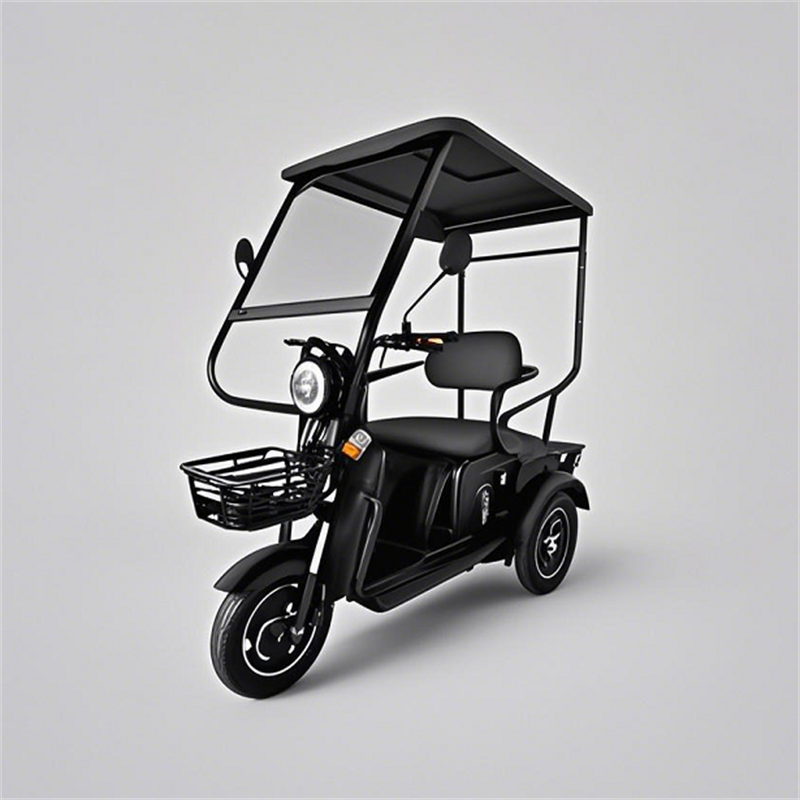
Why is the Manufacturing Process for a Cargo Bike More Complex?
The assembly of a cargo bike is a more hands-on, labor-intensive process than that of a standard bicycle. The unique shapes and sizes of the frames mean they don’t fit into the same automated jigs and assembly lines. This is where the difference in economies of scale really becomes apparent.
Our factory produces a wide range of electric vehicles, and I can tell you that the cargo bike line requires more space and more skilled technicians. The frames are large and unwieldy, requiring specialized welding techniques to ensure strength at every joint. Installing the steering linkage on a front-loader or the differential on a tricycle is far more complex than attaching a simple fork. Wiring the electrical system, with its various sensors, lights, and display, must be done meticulously by hand.
Because the cargo bike market, while growing, is still smaller than the market for, say, a standard mountain bike, the manufacturing processes are less automated. Lower production volumes mean that the fixed costs of setting up the production line are spread across fewer units. This leads to higher unit costs for each cargo bike that rolls off the line, another of the key elements that contribute to the high price for a quality machine.
How Do Shipping, Tariffs, and Logistics Contribute to the Final Price for an Importer?
David, this is a part of the cost that you are intimately familiar with, but it’s worth explaining for the broader context. My job doesn’t end when the cargo bike leaves the factory. Getting these large, heavy products from our facility in China to your warehouse in the USA is a significant logistical and financial challenge.
- Freight Costs: A cargo bike is big and heavy. It takes up a lot of space in a shipping container. Shipping one cargo bike can cost several times more than shipping a standard bicycle that can be packed more compactly. The recent volatility in global shipping rates has only exacerbated this.
- Battery Regulations: Shipping high-capacity lithium-ion batteries is a regulatory minefield. They are classified as Dangerous Goods (Class 9 Miscellaneous) and require special packaging, labeling, and documentation. This adds complexity and cost to every single shipment.
- Tariffs: The final landed cost of any imported product is affected by customs duties and tariffs. These taxes, which can change based on trade policies, are paid on the value of the goods and are a direct addition to your bike cost.
These back-end costs are substantial. When a customer sees a cargo bike in a shop with a high price tag, they are not just seeing the cost of the materials and labor. They are also seeing the accumulated costs of getting that specific product safely and legally across the world.
Can I Find a Cheap Electric Cargo Bike That is Still Reliable?
This is the million-dollar question. The quest for a cheap cargo bike, especially a cheap electric cargo model, is understandable. Affordability is a major factor for many families and businesses. However, this is where a buyer—and a distributor—must be extremely cautious. “Inexpensive” can quickly become “cheap and dangerous.”
From a manufacturing standpoint, hitting a very low price point requires cutting corners. These cuts often come from the most critical areas:
- Battery Quality: Using non-certified, generic battery cells is the number one way to lower costs. This dramatically increases the risk of failure or fire.
- Motor and Brakes: A less powerful hub motor might be used instead of a capable mid-drive, and lower-quality mechanical brakes might be used instead of hydraulic ones. This compromises the entire riding experience and, more importantly, safety.
- Frame and Components: Thinner-gauge steel or lower-quality welds might be used, which could lead to frame failure under a heavy load.
Instead of searching for “cheap,” I advise my partners to search for “value.” There are budget-friendly and affordable options on the market that offer a great balance of price and quality. These bikes, like our YONSLAND X1 new 3 wheels electric ebike, may not have all the bells and whistles of a top-tier brand like Tern or Yuba, but they are built with safety-certified components and reliable drivetrains. It’s always better to invest a little more in a product with a solid frame, good brakes, and a certified battery. Another option for end consumers is looking for a second hand bike, but for a business, the warranty and support that comes with buying a new product is essential.
What is the Long-Term Value? Is a Cargo Bike Worth the Investment?
This is the final, and perhaps most important, piece of the puzzle. The high initial bike cost can be intimidating, but a quality cargo bike is an investment that can pay for itself many times over. The conversation needs to shift from “cost” to “value.”
Consider the potential savings from replacing a second car:
- No Fuel Costs: Electricity to charge an Ebike Charger Battery is a fraction of the cost of gasoline.
- No Insurance or Registration: In most places, these recurring costs are eliminated.
- Minimal Maintenance: A cargo bike is far simpler and cheaper to maintain than a car.
- No Parking Fees: A huge saving in urban environments.
When you add up these savings over a few years, the cargo bike often comes out ahead. But the value goes beyond money. It’s the joy of riding with your kids in the front cargo box, the health benefits of integrating exercise into your daily routine with pedal power, and the positive environmental impact. For a business, an electric cargo bike can dramatically lower delivery costs and improve operational efficiency. So, yes, the initial outlay is significant, but the long-term value makes a cargo bike worth the investment.
What Future Trends Might Affect Cargo Bike Costs?
Looking ahead to the next few years, including 2023 and beyond, we can expect to see several trends that will role in determining the cargo bikes cost. As the e-cargo market matures and demand increases, particularly for last-mile delivery, we should see better economies of scale in manufacturing processes. This could lead to a gradual decrease in the base cost of frames and components.
Advancements in battery technology will also play a crucial role. As energy density improves and production scales up globally, we may see battery costs come down without compromising on safety or range. Similarly, motor technology continues to become more efficient and refined.
However, the demand for more features—like integrated GPS, better suspension, and more sophisticated software—could offset some of these savings. As a cargo bike manufacturer, my focus is on leveraging new technologies to improve performance and reliability while actively working to manage costs. The goal is to continue to provide high-value, durable, and safe mobility solutions that meet the specific needs of your market, David. The future for the cargo bike is incredibly bright.
Key Takeaways to Remember
- Specialized by Design: A cargo bike is a purpose-built utility vehicle, not just a big bicycle. Its high cost comes from stronger frames, better brakes, and heavy-duty components designed to safely carry heavy loads.
- The Electric Premium: The electric cargo bike adds a powerful motor and a high-capacity, safety-certified battery, which are two of the most expensive parts of the build.
- Hidden Costs: The price includes significant investment in research and development, rigorous safety testing and certification, and complex, labor-intensive manufacturing.
- Logistics are a Factor: The bulky size of a cargo bike and the regulations around shipping batteries add substantial cost before it even reaches a distributor.
- Value Over Price: The smartest approach is to look for long-term value, not the lowest price. A quality cargo bike is an investment in safety, reliability, and convenience that can save thousands of dollars over time compared to a car.
Post time: Jul-04-2025